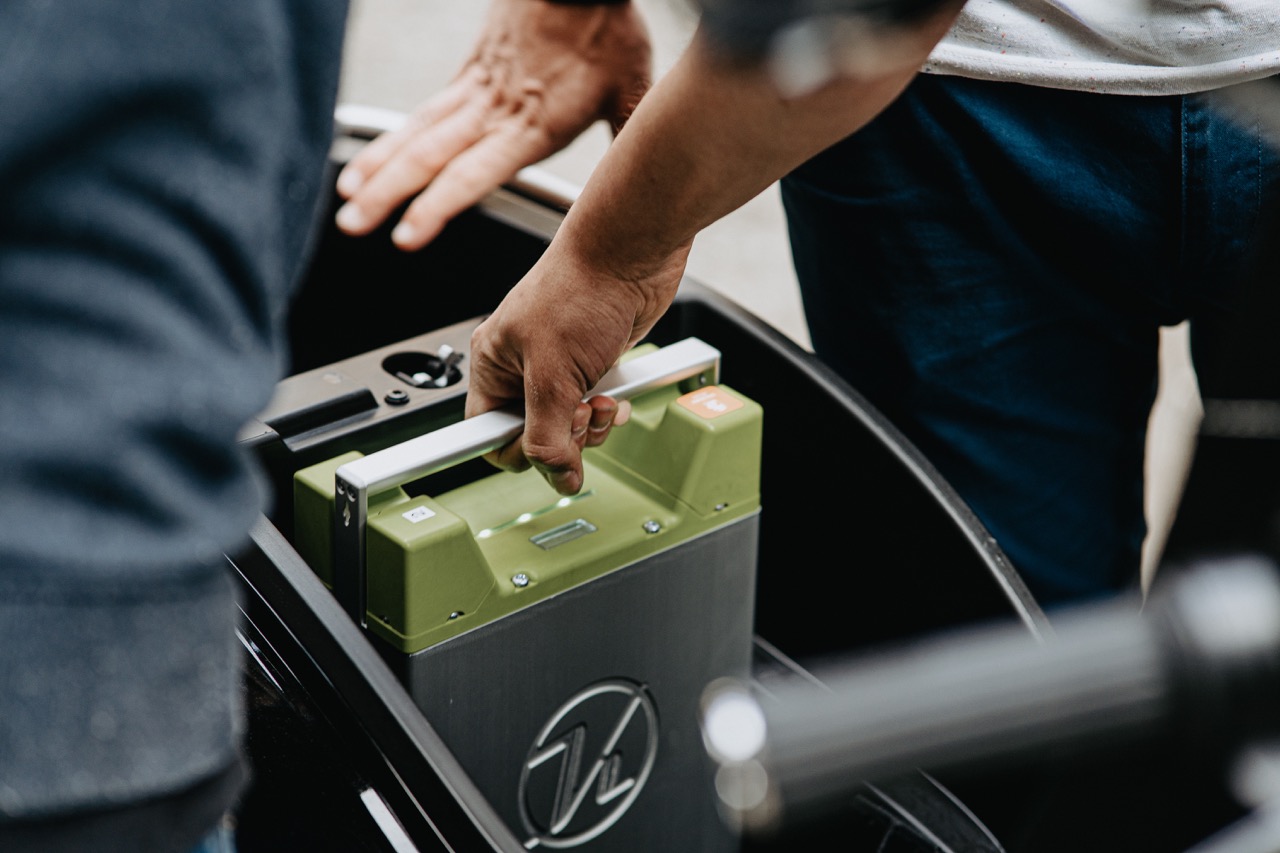
Entre innovation et durabilité, quel futur pour les batteries lithium-ion ?
Quel futur pour les batteries lithium-ion ?
Les batteries sont au cœur du fonctionnement des véhicules électriques et représentent environ la moitié de l’empreinte écologique du cycle de vie d’un véhicule. Malgré des progrès technologiques récents, tous les types de batteries ont des désavantages intrinsèques qu’il sera probablement impossible de gommer avant au moins une quinzaine d’années, ce qui correspond au temps nécessaire à la mise en place de technologies de rupture à un niveau industriel.
Aujourd’hui le modèle dominant est celui des batteries lithium-ion, qui figurent parmi les plus performantes disponibles sur le marché. Elles sont cependant régulièrement sous le feu des critiques : polluantes, inutilisables quand il fait froid, utilisant à outrance de terres rares et autres matériaux critiques et issues de chaînes logistiques peu regardantes des droits humains…
Tour d’horizon des désavantages et solutions potentielles à ceux-ci pour mieux appréhender le futur des batteries.
Les principaux composants de batteries posent de vrais problèmes écologiques
Les batteries lithium-ion regroupent en fait un grand nombre de technologies différentes. La composition finale dépend donc du choix du constructeur. Pour avoir des ordres de grandeur en tête, on peut considérer qu’une batterie de 60kWh est composée de 185kg de minerais.
La composition d’une batterie électrique
- 52 kg de graphite
- 35 kg d’aluminium
- 29 kg de nickel
- 20kg de cuivre et 20kg d’acier
- 10kg de manganese
- 8 kilos de cobalt
- 6 kilos de lithium
- et 5kg de fer
L'extraction de ces métaux est particulièrement problématique : elle nécessite beaucoup d’énergie, est très consommatrice en eau douce, et entraîne une contamination toxique des sols, de l’air et l’eau. Deux métaux font particulièrement parler d’eux : le lithium et le cobalt.
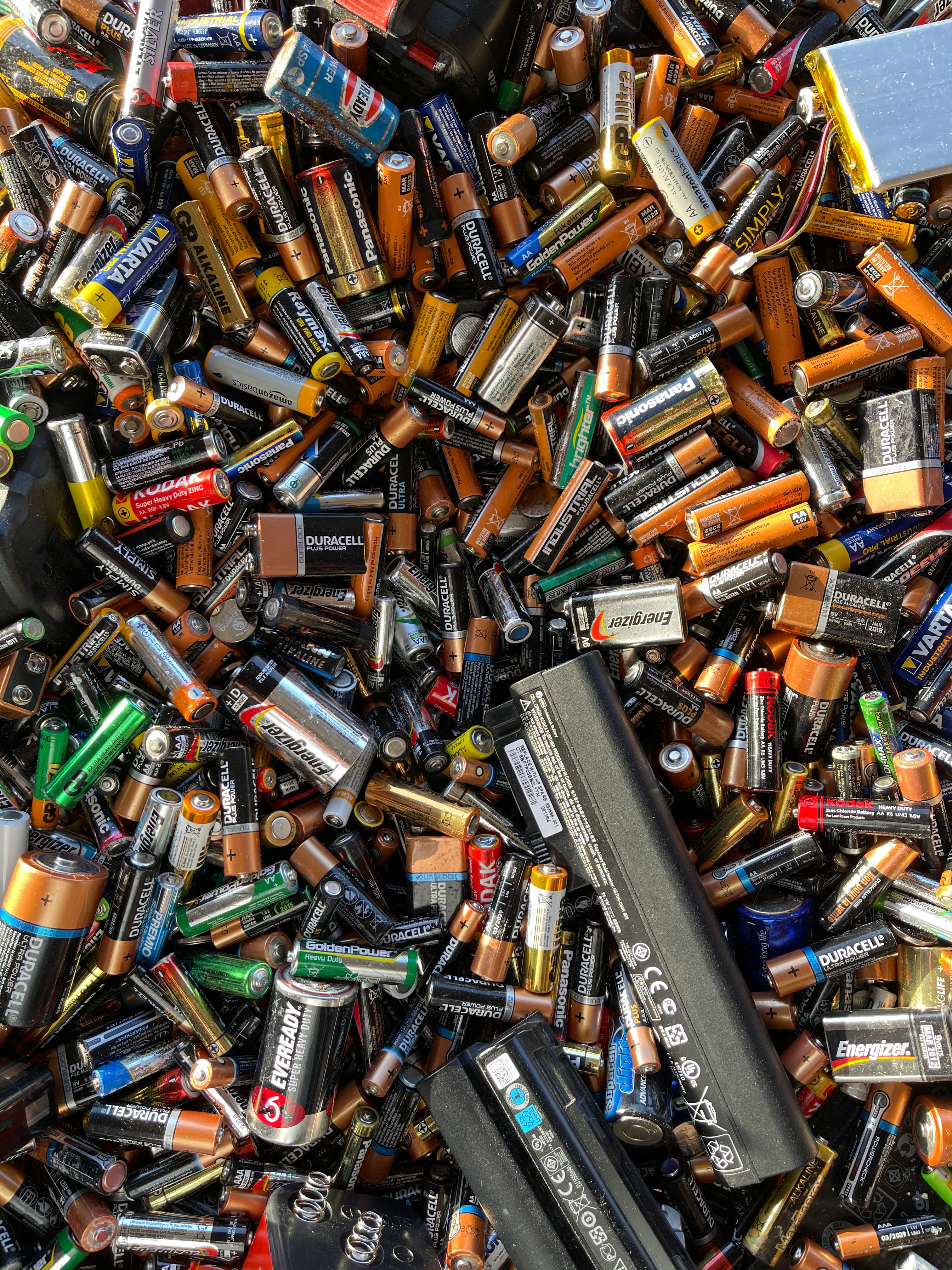
Le lithium : 2000L d’eau pour 1kg ?
Le lithium est un métal principalement présent en Amérique du Sud, se trouvant surtout dans la saumure, un mélange d’eau et de sel présent en profondeur. Pour extraire 1kg de lithium, les techniques utilisées dans les salars du Chili demandent ainsi de pomper jusqu’à 2000L d’eau. Mais on parle ici d’une eau sept fois plus salée que l’eau de mer et inutilisable pour les usages domestiques. Là n’est donc pas le problème comme on peut parfois l’entendre.
Néanmoins, la consommation d’eau douce reste assez exorbitante : le salar d’Atamaca requiert près de 65% de l’eau douce de cette région désertique. De plus, de nombreux additifs chimiques seraient relâchés dans la nature pendant les processus de traitement. Pour autant, le 6 septembre 2023, ce même salar a reçu la certification internationale IRMA qui atteste d’impacts sociaux et environnementaux limités.
Mentionnons aussi les nouveaux procédés d’extraction plus propres en cours de développement. Le projet EMILI qui verra le jour dans l’Allier en 2027 en est un exemple : ce sera une des plus grandes mines européennes de lithium censée permettre la production de 700 000 batteries par an. Mais la concentration naturelle du lithium dans le réservoir est d’environ 1%, ce qui signifie qu’il faut extraire 100 tonnes de roche pour produire une tonne de lithium.
Clairement, les mines de lithium ne seront donc jamais des merveilles écologiques. Mais fallait-il attendre leur relocalisation en France pour s’en rendre compte ?
L’extraction du cobalt au Congo et au Maroc
L’extraction du cobalt pose également problème, moins à cause de l’impact écologique que des conséquences sociales désastreuses.
En effet, le principal exportateur de ce métal est la République démocratique du Congo qui détient près de 73% du marché mondial. La grande pauvreté de la région associée à un cours du cobalt qui a fortement augmenté n’est pas sans conséquences. D’après des rapports d’Amnesty International, ce sont près de 40.000 enfants qui travailleraient dans les mines où des drames humains s’enchaînent quotidiennement. La ville de Kolwezi, située dans la province du Lualaba, au sud du Congo, concentre à elle seule 4 sites miniers. L’expansion des mines industrielles à ciel ouvert, a entraîné l’expulsion des populations voisines portant atteinte à de nombreux droits humains. En septembre dernier, dans son rapport “RDC : alimenter le changement ou le statu quo ?”, Amnesty International revient sur toutes les violations du gouvernement et des opérateurs miniers, pour étendre ses sites d’exploitation.
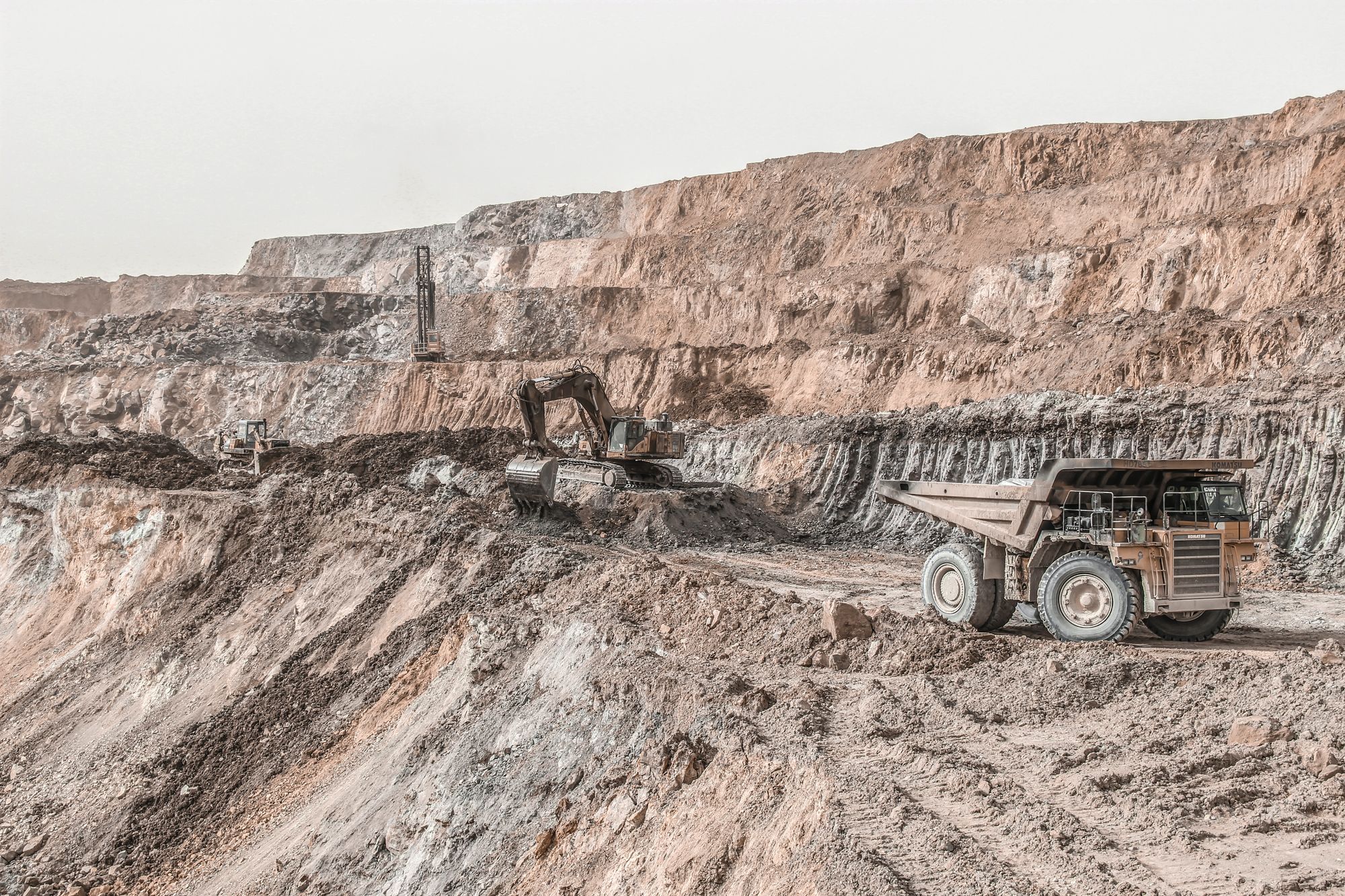
Le pays possède des ressources minières qui en font un acteur clé dans la transition hors des énergies fossiles et dans l’accélération du déploiement des véhicules à faibles émissions. Cependant, Agnès Callamard, secrétaire générale d’Amnesty International, a souligné que les droits humains ne doivent pas être négligés dans le processus d’extraction des minéraux nécessaires à la décarbonation de l’économie mondiale.
Cela préoccupe certaines multinationales comme BMW ou Tesla, qui ont tenté tant bien que mal d’améliorer la situation. Il y a quelques semaines, le groupe bavarois a ouvert une enquête auprès de son fournisseur marocain Managem (aussi fournisseur de Renault), accusé de rejeter de l’arsenic dans la nature et de ne pas respecter les normes de sécurité des travailleurs. La société de propriété royale, qui exploite depuis près de 100 ans le site de Bou-Azzer au Maroc, a déclaré dans un communiqué de presse du 15 novembre 2023, appliquer “les standards internationaux les plus élevés en matière de protection de l’environnement, de pratiques sociales et de gouvernance”. Pourtant, l’enquête révèle une concentration très élevée d’arsenic (entre 40 et 1800 fois les seuils autorisés) dans les sols environnants au site minier, et le manque de protection respiratoire des travailleurs.
Quelles solutions ? Ou alternatives ?
L’importance du recyclage
Afin de limiter l’ampleur des problèmes causés par l’extraction des matériaux indispensables à leur fabrication, on comprend la nécessité de mettre en place un recyclage efficace des composants des batteries. Ce marché en est seulement à ses prémices, mais il se met peu à peu en mouvement. Depuis le début des années 2000, les constructeurs français ont déjà l’obligation de gérer le recyclage de toutes les batteries de leurs véhicules, même si la chaîne logistique n’est pas encore tout à fait mature. Une directive européenne impose à la filière automobile un taux de réutilisation et de valorisation des VHU (Véhicules Hors d’Usages) de l’ordre de 95% du poids moyen par véhicule et un taux de réutilisation et de recyclage à 85%.
Plusieurs facteurs peuvent nous faire espérer un recyclage plus efficace à l’avenir :
- Il n’y a aucune vraie limitation technologique au recyclage complet des batteries
- Le prix des matières premières des batteries devrait continuer d’augmenter à cause de la forte demande de véhicules électriques
- La réglementation européenne impose que 90% du cobalt et du nickel et 50% soient recyclés en 2027 (respectivement 95% et 80% en 2030)
La filière française se met ainsi déjà en marche : citons les sites d’Eramet à Dunkerque ou de Li-cycle dans les Hauts-de-France. Certaines technologies de recyclage sont déjà bien en place et maîtrisées comme celles du recyclage du plomb et du nickel : le lithium devrait suivre la même trajectoire au vu de sa forte utilisation dans les batteries des véhicules.
Pour résumer, la chaîne logistique et les technologies de recyclage des matières premières au sein de nos batteries pourraient devenir matures au cours des prochaines années, au fur et à mesure que le marché se structure et que les réglementations se durcissent. D’après l‘AVERE, le recyclage des métaux demanderait 25 à 50% d’énergie en moins, comparé à l’extraction des matières premières. Une solution concrète, qui permettrait donc de réduire considérablement nos émissions de CO2 et nos déchets.
Vers une production plus locale ?
Le déploiement massif des véhicules électriques pousse les industriels à repenser la production vers des modèles plus locaux. Aujourd’hui, la Chine domine le marché avec près de 75% des parts de marché. Récemment la start-up française Verkor a lancé à Dunkerque le chantier de sa première Gigafactory pour produire des batteries françaises : une alternative bas-carbone étant données les faibles émissions de la production d’électricité en France. Dans un premier temps, l’entreprise fournira Renault avec l’objectif de produire deux millions de véhicules électriques en France en 2030. Le constructeur français s’est engagé à acheter 75% de la production de Verkor, pour utiliser ces batteries dans les futurs modèles Alpine, et les segments supérieurs de la gamme Renault.
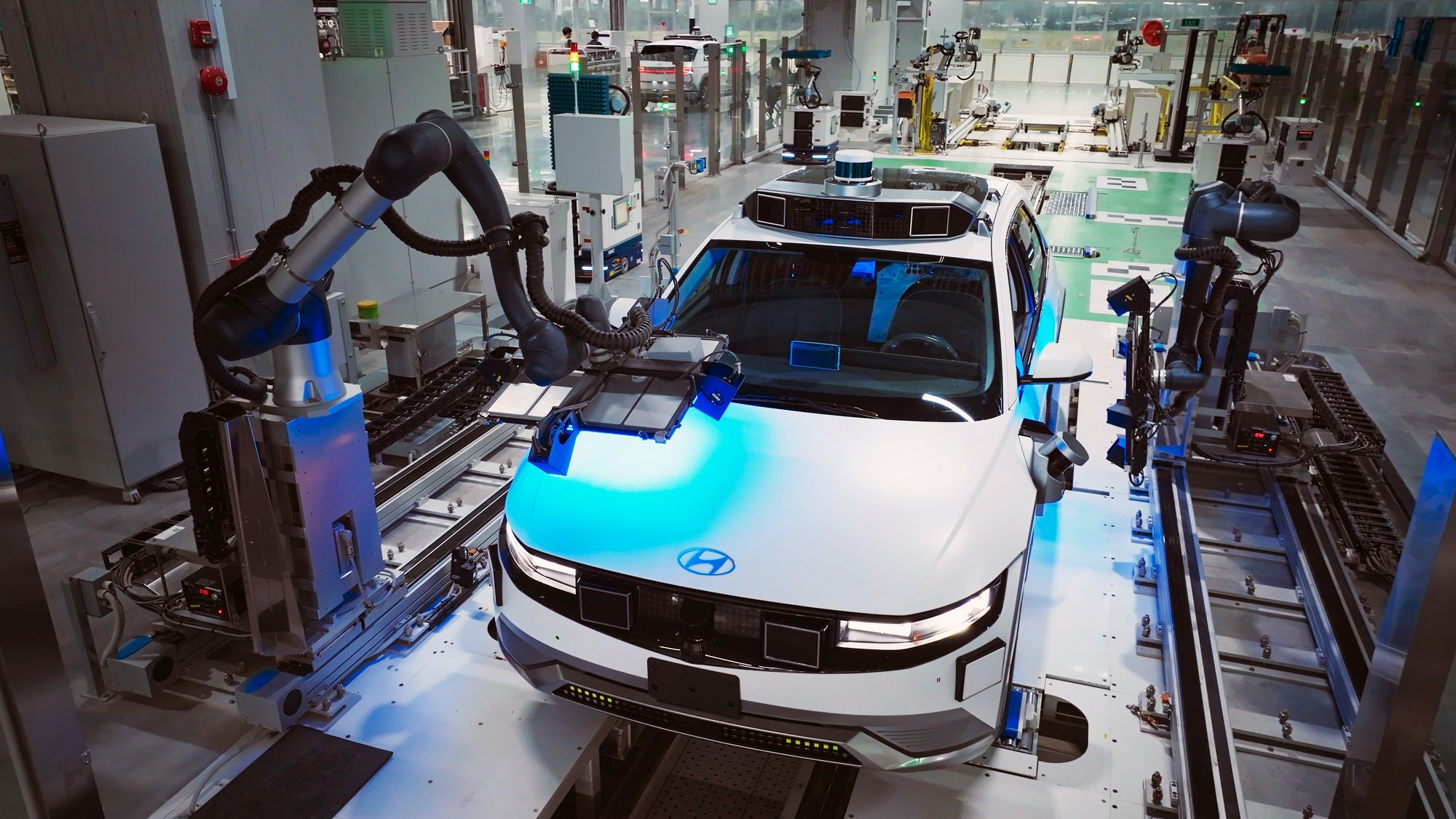
Déjà nommé “la vallée de la batterie”, le nord de la France est aux premières loges pour assister à la réindustrialisation de la filière automobile. D’autres Gigafactory devraient voir le jour dans les années à venir :
- Automotive Celles Company, la coentreprise de Stellantis, TotalEnergies et Mercedes a ouvert ses portes à Douvrin/Billy-Berclau en mai dernier.
- L’entreprise taïwanaise ProLogium a bénéficié d’une subvention de l’État de 1.5 milliards d’euros pour implanter, à Dunkerque, sa première Gigafactory prévue pour la fin d’année 2026.
- Au sien du pôle Renault ElectriCity (regroupement des usines de Douai, Ruitz et Maubeuge), c’est le groupe AESC-Envision qui construit son usine de batteries, qui devrait être opérationnelle à partir de 2024.
Au total, ce sont 4 projets en France, pour une cinquantaine en Europe. L’Allemagne largement en tête a accueilli les projets de Tesla, et plus récemment du suédois Northvolt.
Cependant, même si la course pour rattraper l’industrie chinoise semble bien engagée, elle demeure difficile à remporter. D’une part, l’avance est considérable, et d’autre part la Chine dispose de ressources nationales exploitables. En Europe, c’est le Portugal qui détient les plus grandes ressources sous-sols de lithium mais qui ne seront pas exploitables avant plusieurs années, en raison des procédures d’autorisation. L’UE semble donc encore bien dépendante des pays comme la République démocratique du Congo, qui extraient l’essentiel du cobalt, nickel, lithium, manganèse et graphite, nécessaire à la production des batteries lithium-ion.
Et par rapport à une voiture thermique ?
Les véhicules électriques sont donc loin d’être parfaits. Mais assurément, ils restent sans équivoque une meilleure solution que leurs équivalents thermiques, même sans considérer l’ensemble de leur cycle de vie.
Rappelons quelques faits essentiels dans la discussion :
- Les véhicules électriques ont besoin de moins de matières premières. En prenant compte du recyclage de la batterie et de la majeure partie des métaux qu’elle contient, un véhicule électrique consomme 30kg de métaux pour sa batterie li-ion. Pour une voiture à combustion, c’est en moyenne 17 000 litres d’essence qui sont brûlés au cours de son cycle de vie.
- Les batteries lithium-ion ne sont pas encore optimisées, et d’ici une dizaine d’années les avancées technologiques devraient réduire de moitié la quantité de lithium nécessaire et de trois quarts celle de cobalt. En parallèle des batteries NMC (Nickel, Manganèse, Cobalt), les batteries LFP (Lithium, Fer, Phosphate) sont en train de se développer pour les véhicules à plus faible autonomie. Ces batteries ne requièrent pas de cobalt pour leur production.
- En parlant du cobalt : il est beaucoup utilisé pour les électrodes des batteries, mais est aujourd’hui encore largement utilisé dans l’industrie pétrolière. Le pétrole brut contient une faible part de soufre (entre 0,1 et 2,5%) que les pétroliers sont dans l’obligation de retirer. En se liant à l’humidité dans l’air, le soufre devient de l’acide sulfurique, responsables de nombreux problèmes pulmonaires. L’extraction du soufre lors du raffinage est alors exercé par un catalyseur à base de cobalt, qui se dissoudra dans le diesel et se retrouvera dans le carburant disponible à la pompe.
- Comme les véhicules électriques, les véhicules thermiques nécessitent eux aussi des terres rares comme du palladium ou du platine pour leurs pots catalytiques notamment.

Résumons nos apprentissages !
L’exploitation des ressources minières est un enjeu majeur dans la transition énergétique, notamment en ce qui concerne la production des batteries destinées aux véhicules électriques. L’aluminium, le graphite, le nickel, le cobalt et le lithium sont des composants essentiels à cette production. Leurs extractions engendrent de graves conséquences sociales et environnementales sur les zones exploitées au Congo, au Maroc, ou encore au Chili. Pour limiter l’extraction de ces métaux et les émissions de CO2, il est alors primordial pour les industriels d’intégrer une part croissante de matériaux recyclés à leurs chaînes de production, ce qui devrait avoir lieu dans les années à venir. Par ailleurs, la Chine est toujours leader sur le marché des batteries avec 75% de parts de marché : pour se détacher du leadership chinois, l’UE a investi des milliards d’euros pour construire des Gigafactory sur le sol de ses pays membres. En France, on dénombre déjà quatre projets d’usines de production de batteries hautes technologies, toutes implantées dans le nord du pays. Enfin, bien que les véhicules électriques ne soient pas parfaits, ils restent cependant une bien meilleure alternative à leurs homologues thermiques.
« Dans tous les cas, il est clair que l’impact social et environnemental du réchauffement climatique est catastrophique et d’une ampleur bien plus importante que celui de l’extraction minière pour les batteries ».
Georg Bieker, chercheur à l’ICCT.